As we all know, clutches in current markets were invented by Borg & Beck company in about 1925. Except modification on friction materials and use of multiple discs, the other components still remain unchanged, namely clutch disc, pressure plate and release bearing.
Need generates most of changes, notably in motorsports, in order to deal with more horsepower. Apparently, heavier clamping pressure makes the extra capacity in single-plate clutch, which would increase pedal effort and might lead to inconvenience.
If friction material is same, the only method to generate more torque capacity is adding clamp load. More clamping pressure is needed to prevent disc from slipping. In such a circumstance, driver can get a very heavy clutch pedal and even has to use two feet to press it. What you can do subsequently is adding one more disc, hence you can get four surfaces instead of two. At this point, floater plate is needed in between, which can take and double torque capacity.
In order to get more horsepower, more clamping pressure or surface area is needed. More clamping pressure is for single-plate clutch and more surface area is for dual-disc clutch.
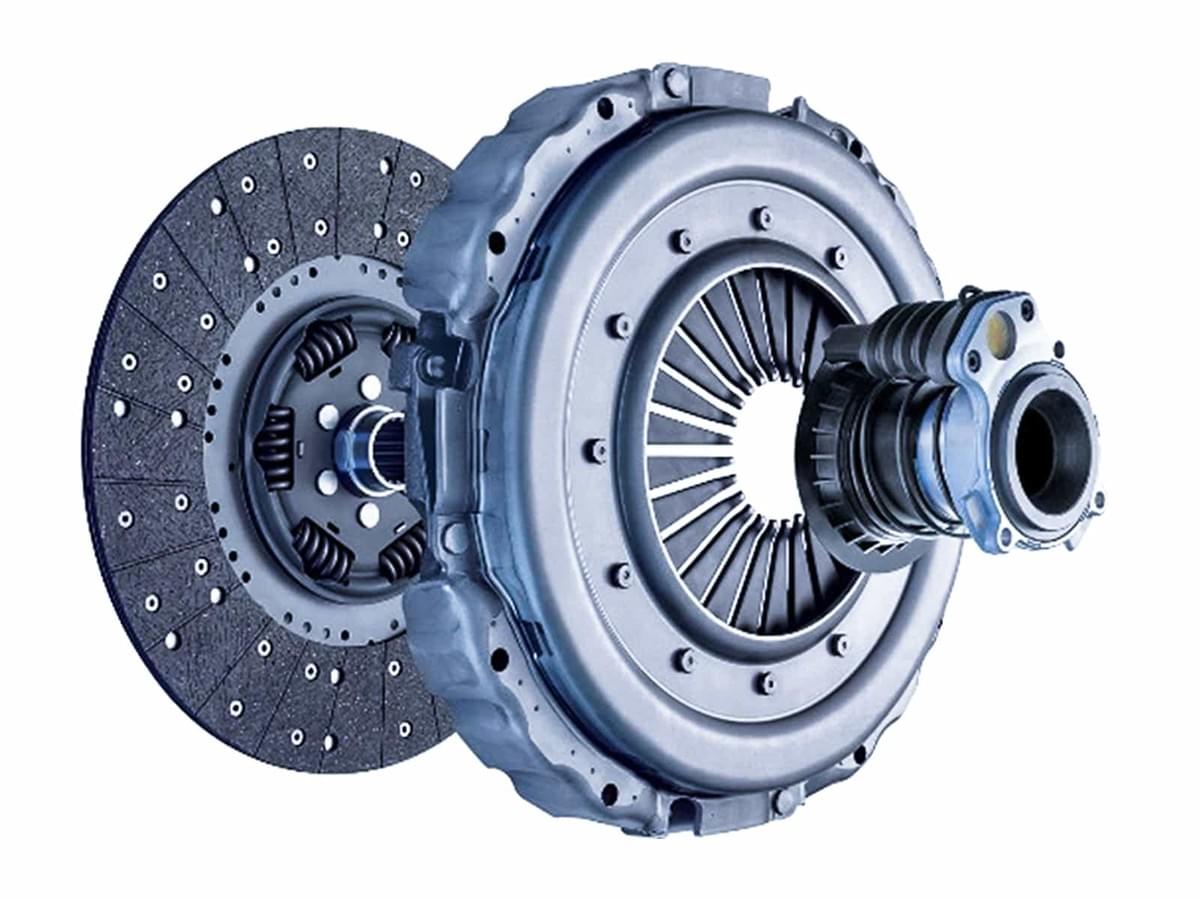
Some companies have developed dual-disc clutches for V8 engines, namely V8 by GM, Ford and Chrysler. These clutches, however, are not suitable for smaller engines that have big power as well.
In fact, some certain new twin-disc clutches are invented for these smaller engines. The forged twin clutch line uses a forged aluminum cover with reinforced extra rigidity, stability and higher efficiency, which means more clamping load can be added with less pedal effort.
Yet, what makes forged twin clutch special is not only the pressure plate, but the hub and friction surface system. The forged twin clutch has a single hub driven by both discs, instead of using two separate discs, which are rigid for racing or sprung for street use.
Thicker splines are added to the outside of the hub, in the meanwhile, matching splines are also incorporated on the inside of the friction surfaces, solid or sprung. In essence, the twin-disc clutch is reinvented by separating the friction surface from the hub and making parts completely modular. Pressure plate design can accommodate sprung and unsprung hubs, organic, full circumstance materials and cerametallic “pucks”. This technology is as old as spline, but it proves to be a brand new application for it.