There exist three fundamental kinds offlywheel usually identified in vehicle engine and each one needs a differentmachining approach.
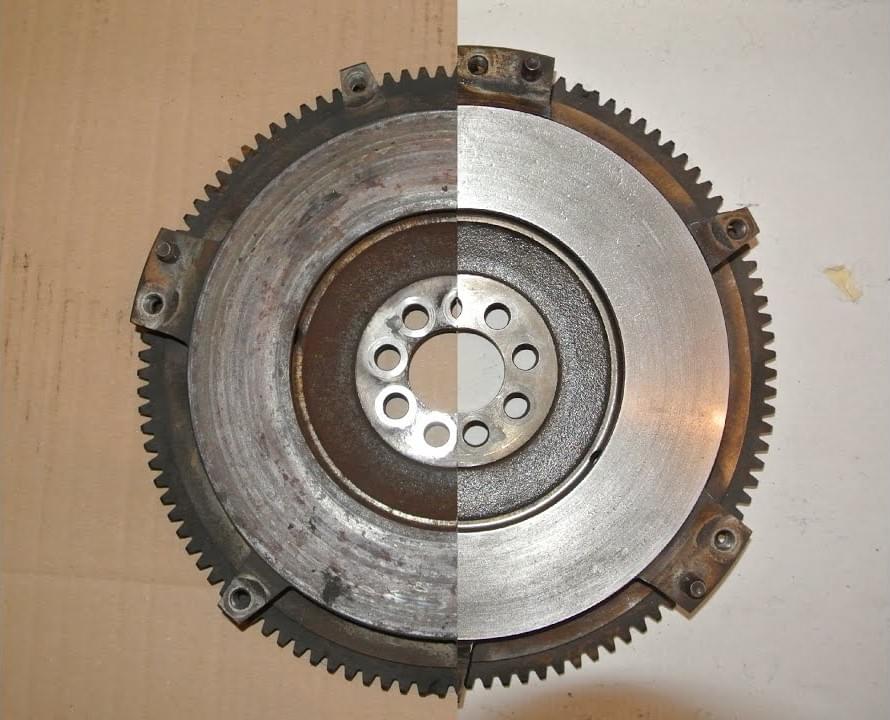
Flat type
For this type, clutch disc and cover areinstalled on the same surface and are at same height. This provides a singlewider area which can be machined by using a larger separate grinding wheelwhich is used for other main operations.
Recessed type
Similarly, clutch disc and cover areinstalled on the same surface and are at same height. However, these twocomponents are subsequently shrouded by a raised peripheral lip or where theclutch face is on a lower surface height than the cover face. This provides impressionof clutch disc being sunk into flywheel.
In another case, single large grindingwheel is unlikely to be used. A further attachment for installing a smallerflared grinding wheel is needed. This attachment is installed into the centreof large grinding head, and enable a smaller diameter tapered grinding wheel beused. The taper on this wheel makes itbe able to machine right up to any raised area on flywheel.
If clutch and cover surfaces are atdifferent height, both have to be machined by exactly equal amounts. This aimsto maintain the tension of cover against the disc when in operation and preventslipping.
Raised type
In terms of this type, the surface ofclutch disc is at a raised position compared with that of cover.
In this situation, both surfaces have tobe machined equally for the reasons mentioned above. The same tapered grindingwheel is used for this flywheel type’s grinding operation. The worn raisedclutch face is machined firstly prior to the area that carries the clutch coverbeing reduced to the original depth.