Flywheels that are damaged due to wear or overheating can be restored by re-grinding damaged surfaces. We ZNDmotor uses refacer and rotary table attachment to conduct the machining operation.
When does a flywheel need refacing?
You can find wear or damage on the surface of a worn or damaged flywheel, with which the clutch friction plate is contacted. Damage that is apparent includes scoring, deeper grooves which are made when clutch disc is slipping or is worn over the limit, and raised hot spots which are formed when the surface of clutch is overheat.
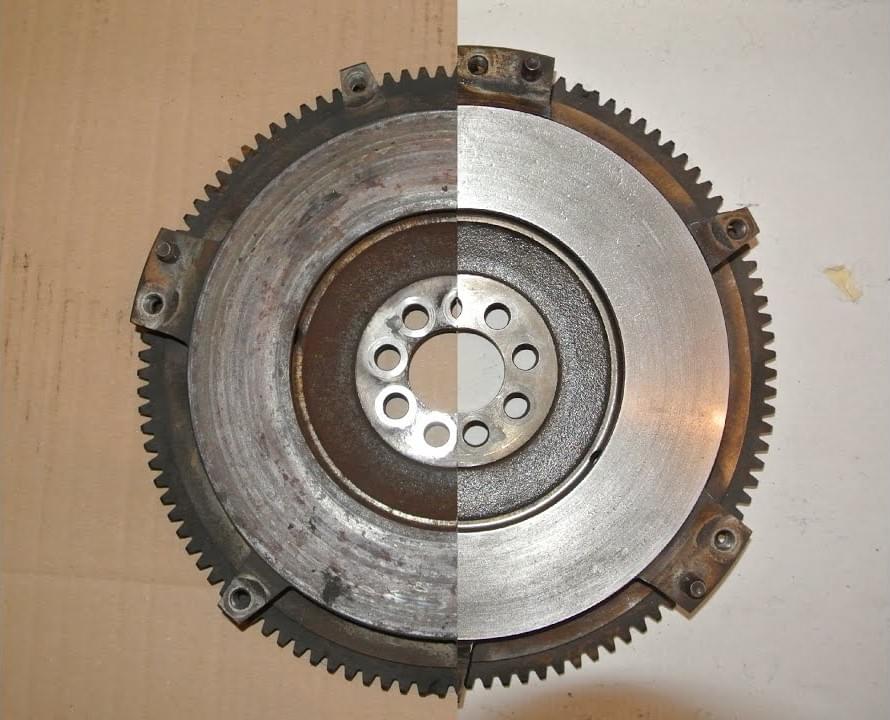
Refacing the flywheel
With the rotary table installed on the refacing machine, the flywheel is put onto the rotary table, checked that the mounting face is clean and true. This step can make sure that the flywheel can be clamped down squarely prior to commencing machining. This step is also vitally important, since the flywheel that is machined out of true can lead to bad clutch action when in operation.
When on the table, the flywheel will be centered by using a dial gauge. This is to ensure the flywheel can run concentrically with grinding wheel when machining is conducted. When centered, the flywheel is clamped into position for grinding operation.
The wheel head is lowered until the grinding wheel is positioned slightly over the face that is to be machined. When all safety guards are ready, the grinding spindle and rotary table can be started. The rotate is in opposite directions, hence the grinding wheel cuts into work piece, instead of attempting to skid along over it. The coolant pump is switched on and the grinding wheel fed down to the job with the graduated in-feed dial. When contacted, the feed can be maintained manually, gradually increasing the cut until all the damages on flywheel surface are removed.
After refacing, the flywheel can be benefited from balancing or lightening, depending upon specific engine type and application.